Whether they’re on a helmet, a surface control system, or hose, they are one of the most critical components in your system.
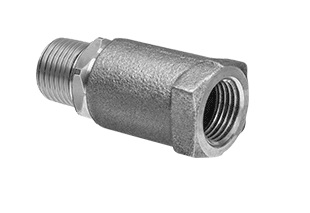
If you didn’t get a chance, take a look at an old Myth Busters episode segment on Youtube (https://youtu.be/LEY3fN4N3D8) to see just how important it is. I use this segment as a training evolution at my company. If that doesn’t make the point to a new diver or tender, nothing will.
If you look at Kirby Morgan, for instance, you are to test the one way-valve every diving day. On their daily check list, it states “Orally check the One-Way Valve. With the steady flow valve open, orally blow air thru the one-way valve. Air should pass freely. Next suck back on the umbilical adapter, no air should pass back thru the one-way valve and umbilical adapter. If air can be drawn back thru the one-way valve, the one-way valve will require overhaul or replacement.”
You probably know all of this already, right? It’s drilled into everyone at dive school.
Since we inspect and repair hundreds of helmets each year, we are bound to see some odd problems. One example of what we’ve encountered in regards to helmet one-way valves involves a bit of moisture and the weather. The situation involved a helmet with a mystery problem. When the hat is out in the field, the one-way valve was failing in the morning daily check. When the client would bring the helmet in, everything worked as designed. Go figure… They would return to the job site and within a day or so, it would fail again.
The helmet was returned a second time and we opened up the one-way valve, this time water poured out of it. It turned out that the breathing air compressor didn’t have a moisture separator installed and the client would put the helmet in the trunk of his car at the end of the diving day, which was parked outside in sub freezing weather. So the water would freeze in the valve and the valve would fail (either it wouldn’t shut when tested or would freeze closed). So water did what water does. If you’re finding the same issue, check the valve for water intrusion.
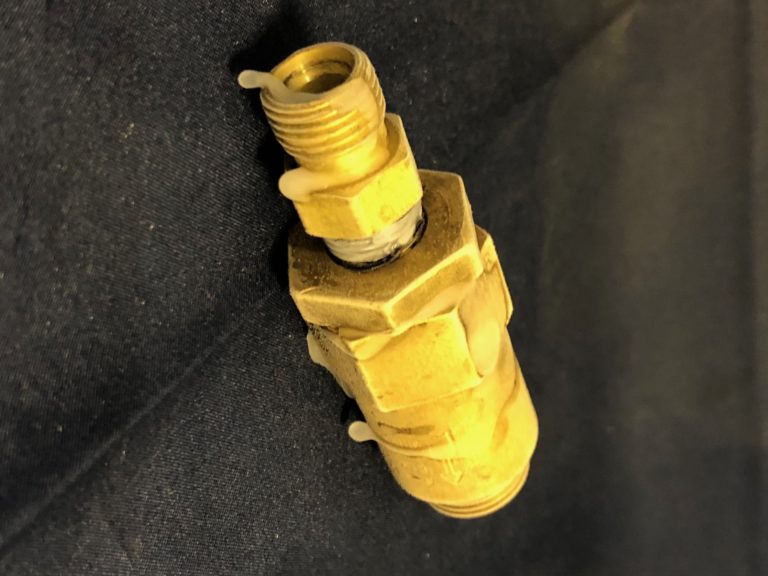
Along with the daily test, regular maintenance is important. Make sure that any o-rings that may be installed are checked and/or changed at regular intervals. You will want to visually check that the valves are cleaned and maintained to the standard that the manufacturer outlines in their documentation. Confirm that you document any maintenance so that the next person knows there was something done. I know it’s no one’s favorite task but it will sure save a lot of trouble in the long run with your audit or (hopefully this never happens) a dive accident.
My motto with these kinds of components is – if in doubt, replace it. They are relatively inexpensive and it’s a type of insurance that breathing gas is not going to end up flowing in the wrong direction. It seems obvious but we all get complacent with components that we check day in and day out and we have never seen them fail, until they do.
As always, dive safe.